EMVAL-demonstrator
The EMVAL (engine material validation) demonstrator was created as part of the European Clean Sky 2 technology program to validate new low-pressure turbine technologies. It was developed, built, and tested at MTU Aero Engines in Munich. The test platform was an MTR390 helicopter engine provided by the German Armed Forces.
The focus was on the integration of innovative high-temperature materials and advanced manufacturing processes, as well as on the validation of those materials and processes in the MTU low-pressure turbine and in the adjacent components: the inter-turbine duct and turbine exit case. To this end, a complete power turbined had to be redesigned, built, and mounted on the core engine. The turbine exit case was provided by GKN Aerospace.
Specifically, the partners aimed to optimize and refine the design of new types of high-temperature-resistant materials (such as fiber-reinforced ceramics), innovative manufacturing processes for new disk materials, and additively manufactured components.
Exhibit: EMVAL low-pressure turbine and inter-turbine duct
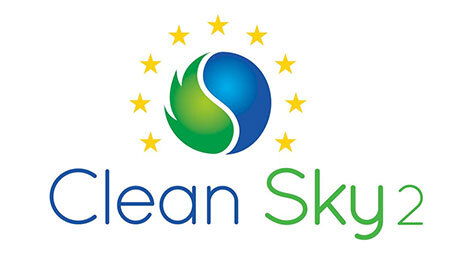
The European Clean Sky 2 technology program ran from 2014 to 2024. MTU was one of the program’s 16 lead companies and cooperated with the two strategic partners, GKN Aerospace Sweden AB and the German Aerospace Center (DLR).
New technologies were developed for the low-pressure turbine (LPT) and high-pressure compressor (HPC) components. These new technologies involved further improved aerodynamics, new, lighter and more temperature-resistant materials, and innovative manufacturing processes. Two demonstrators were set up for the validation. Their innovations were incorporated into the second generation of the GTF™ engine family.
The LPT technologies were validated at MTU in Munich using the EMVAL (engine material validation) demonstrator. In parallel, the two-shaft compressor rig was developed and built at DLR in Cologne in order to demonstrate the new compressor technologies. GKN Aerospace was responsible for the design and manufacture of the low-pressure compressor and inter-turbine duct. The rig is being tested at DLR in Cologne.
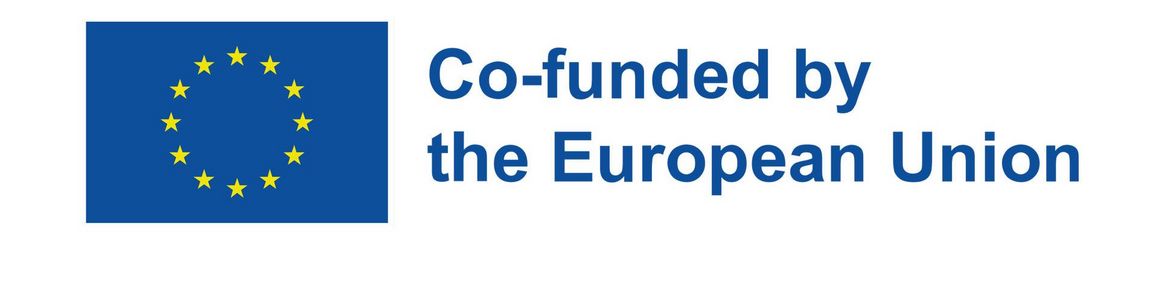