Core competencies
Low-pressure turbine Turbine center frame High-pressure compressor
MTU is the world's technology leader when it comes to low-pressure turbines (LPTs) that operate at maximum efficiency.
MTU delivered is masterpiece in the form of the high-speed LPT for the geared turbofan (GTF): with technology that is unparalled in the world, MTU is the only company to have mastered it for this application. The GTF AdvantageTM is set to receive a more enhanced LPT made by MTU.
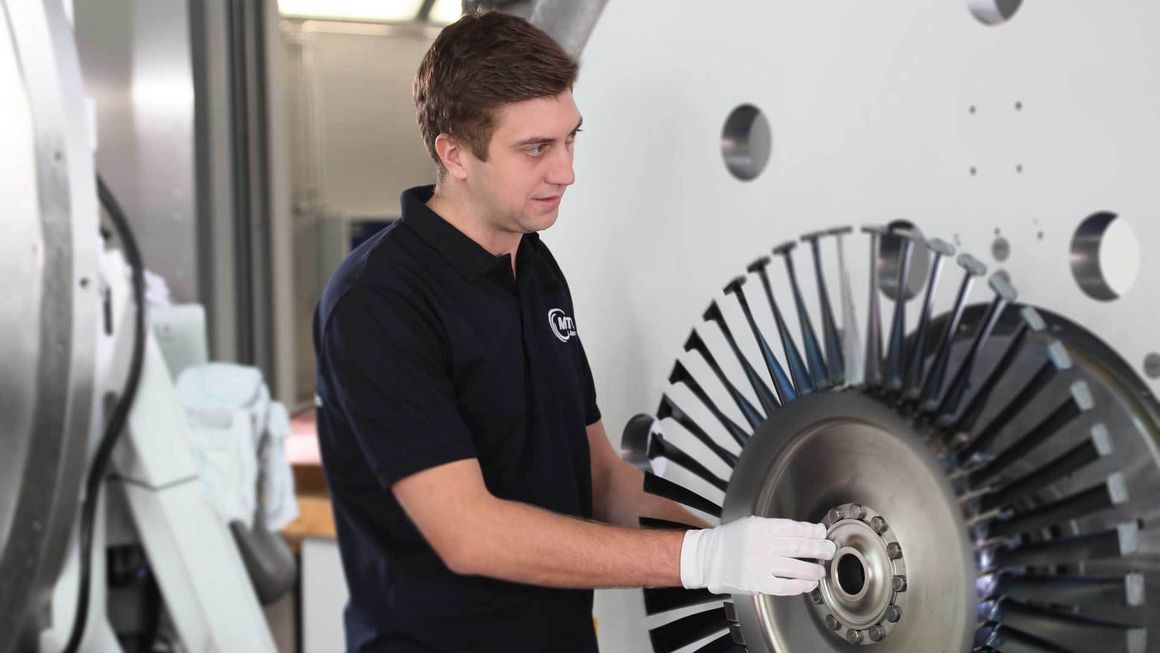
The GTF LPT achieves significantly higher circumferential speeds, which reduces the aerodynamic load and means the stages can work both harder with higher stage efficiencies. This allows the stage count to be reduced by almost half.
For the GTF Advantage, MTU experts are further enhancing the high-speed LPT by, for example, optimizing the gap management system.
For engines in the upper thrust category, MTU manufactures turbine center frames (TCFs). The company develops and manufactures this sophisticated component for the long-haul aircraft engines GP7000 (Airbus A380), GEnx (Boeing 787 Dreamliner and Boeing 747-8) and GE9X, the exclusive engine for the Boeing 777X.
High-pressure compressor
Compressors are the centerpiece of an engine. MTU has been developing, manufacturing and repairing high-pressure compressors (HPCs) for over 50 years. HPC design is the supreme discipline in engine construction. Those who master it are right at the top of the engine league.
MTU initially acquired its expertise in the military sector: it supplies the intermediate-pressure and high-pressure compressors for the Tornado’s RB199 engine, the low-pressure and high-pressure compressors for the Eurofighter’s EJ200 engine, and the intermediate-pressure compressor for the TP400-D6 in the Airbus A400M military transporter.
MTU developed its first commercial HPC for the PW6000, the engine for the A318. The current flagship is the HPC for the eco-efficient geared turbofan (GTF), which MTU developed jointly with Pratt & Whitney. This success story is continuing: starting in 2024, the latest GTF variant—the GTF Advantage™—will feature an even more enhanced HPC.
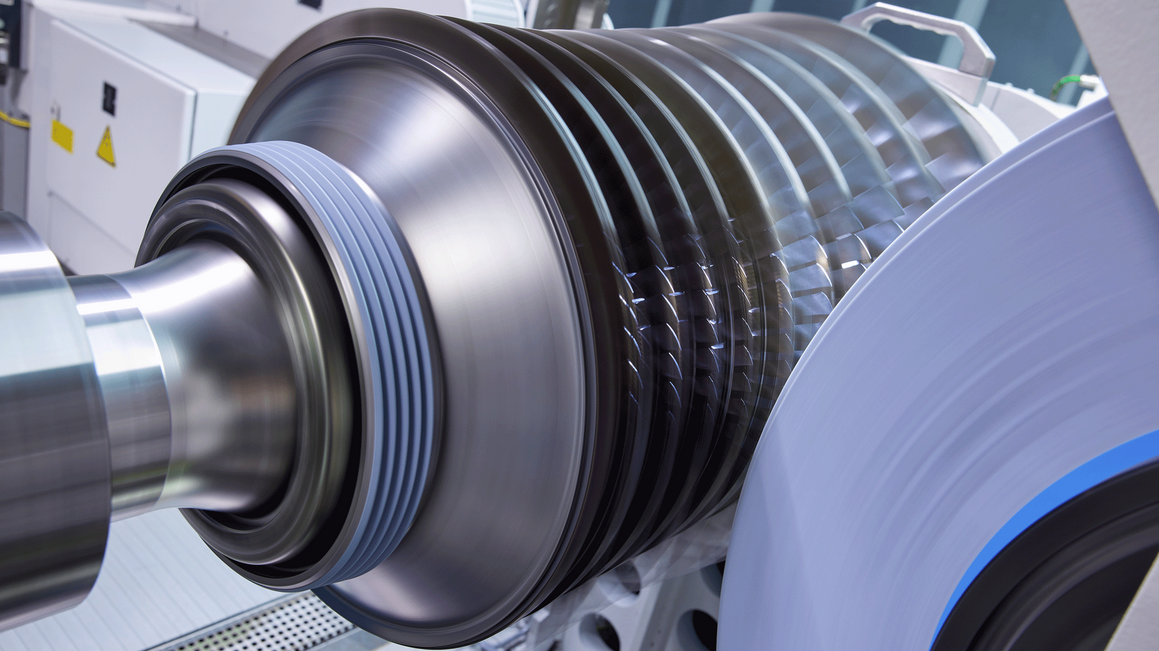
MTU’s involvement in the new European fighter jet, the Next Generation Fighter (NGF), also sees the company continue its tradition of military compressors: for this jet engine, MTU is developing and manufacturing the entire compression system consisting of low-pressure compressor, inter-compressor duct and HPC.
Innovative technologies
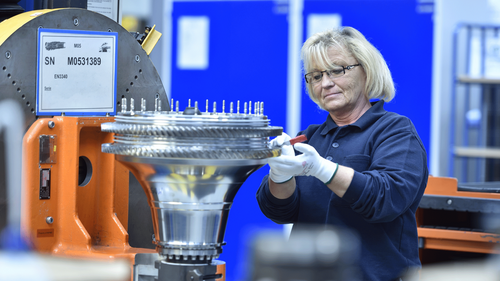
The next generation of high-pressure compressors is already being prepared—supported by sophisticated and ever more refined simulation, calculation and design methods in all analytical disciplines as well as rig and demonstrator tests.
The goal is to achieve a more compact, more lightweight design without sacrificing efficiency. Additional possibilities result from improved interaction between the HPC and the low-pressure compressor in front of it, and the optimized design of the inter-compressor duct. At the component level, additive manufacturing combined with novel bionic design processes enables the optimization of component geometry.
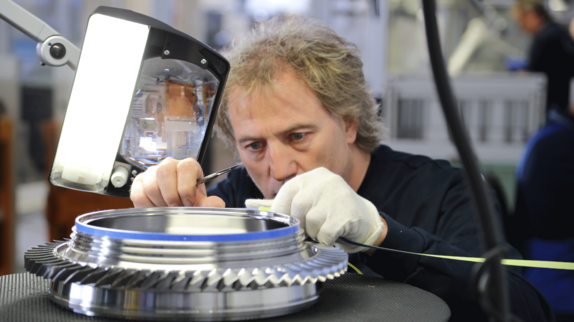
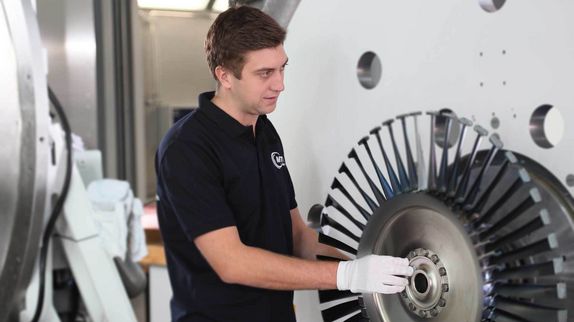