Powering the new European fighter jet
The New Generation Fighter Engine (NGFE) powers the New Generation Fighter, which is the centerpiece of Europe’s Future Combat Air System (FCAS). Together with Safran Aircraft Engines and the Spanish engine and component manufacturer ITP Aero, MTU is developing, producing and providing support for the NGFE. FCAS is expected to be available starting in 2040.
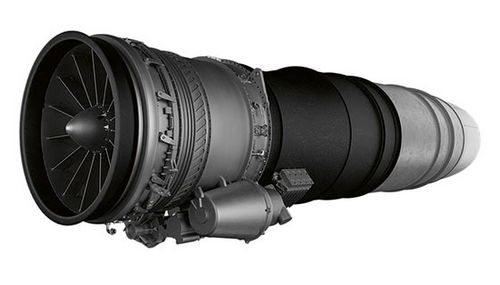
“FCAS is much more than merely an air defense system: it represents Europe’s big chance to reinforce its defense autonomy and to establish and expand its own supply chain for high-tech products. This is why long-term European partnerships are so important."
Michael Schreyögg, Chief Program Officer, MTU Aero EnginesA strong team for Europe’s security
A project of this scale calls for strong partnerships. Under the leadership of their EUMET (European Military Engine Team) joint venture, and in collaboration with ITP Aero, engine specialists MTU and Safran are developing outstanding technologies and engine demonstrators that meet FCAS requirements.
MTU is responsible for its flagship products, the high-pressure compressor and low-pressure compressor and is the lead for all maintenance and service activities.
High-tech for the air force of tomorrow
The New Generation Fighter Engine (NGFE) sets new standards for sixth-generation fighter jets. As the heart of the New Generation Fighter, part of Europe’s Future Combat Air System (FCAS), it combines maximum efficiency, innovative hybrid technologies, and extreme performance. We contribute our expertise in key areas such as compressor technology and engine control—for the ultimate in power, maneuverability, and availability on every mission.
The New Generation Fighter Engine
A glimpse into the future - The New Generation Fighter Engine (NGFE) is supposed to take off in 2040. MTU Aero Engines has a proven military trackrecord in Germany and Europe and is, therefore, ready to be part of the development of the new propulsion system today.