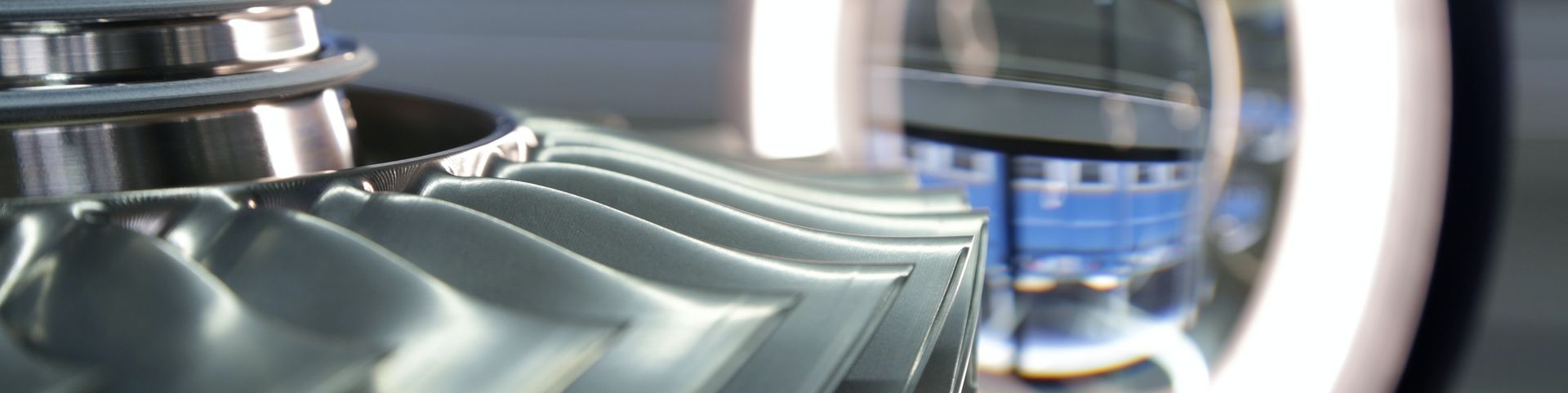
Core competencies
MTU's core competencies
Efficient compressors
Compressors are the centerpiece of an engine. We have been developing, manufacturing and repairing them for decades. Today’s compressors are built on the cutting-edge blisk principle. MTU, in collaboration with Pratt & Whitney, developed the commercial high-pressure compressor for the eco-efficient geared turbofan engine family.
Award-winning turbines
Our expertise covers turbines for business jets, power turbines for transport helicopters, and large, low-pressure turbines for medium- and long-haul jets. Our masterpiece is the high-speed low-pressure turbine of the geared turbofan: its technology is unparalleled in the world.
Turbine center frames
For engines in the upper thrust category, MTU manufactures turbine center frames (TCF). These sophisticated components are exposed to extreme stresses in operation. We build these frames for the GEnx in the Boeing 787 Dreamliner and 747-8, and for the GE9X, the exclusive engine for the Boeing 777X. MTU also produces the GP7000‑TCF.
Testing and instrumentation
MTU’s expertise in engine testing is also unparalleled. On our high-tech test stands, we test materials, coatings, components and entire engines. Only the latest in measurement technology, refined by MTU, is used in these sophisticated and challenging tests.
Revolutionary maintenance
Developed in-house, MTU’s high-tech repairs set worldwide standards in the maintenance of commercial engines and industrial gas turbines, ensuring peerless levels of restoration and long on-wing times. Its CORTEX fleet management software and engine trend monitoring are revolutionary as well.
High-tech manufacturing
MTU is one of the leading blisk manufacturers. Our Munich location is home to one of the most advanced manufacturing facilities for this type of compressor rotor. MTU also demonstrates its expertise in other high-tech manufacturing processes—additive processes, for example, are playing an ever more important role.
Comprehensive systems expertise
Engine control and monitoring ensure the performance, safety and commercial viability of advanced engines. We have more than 40 years of experience in this field. Our product portfolio includes the complete control and monitoring system, as well as electronic and hydraulic subsystems and equipment, including software.